1.4 - 1.5
Coated Electrodes
Coated electrodes are classified according to the coating factor. Coating factor is the ratio of the diameter of the electrode to the diameter of the core wire.
So, following are sub types of coated electrodes:
Light coated electrodes with coating factor of 1.25. Light coating applied to electrodes helps to remove impurities such as oxides and phosphorous. Light coating also helps in enhancing arc stability.
Medium coated electrodes with coating factor of 1.45.
Heavily coated electrodes with coating factor ranging between 1.6 to 2.2. These electrodes have a proper and well defined composition. The heavily coated electrodes are designed in three types – electrodes with cellulose coating, electrodes with mineral coating and the electrodes with coating of both cellulose as well as mineral coating.
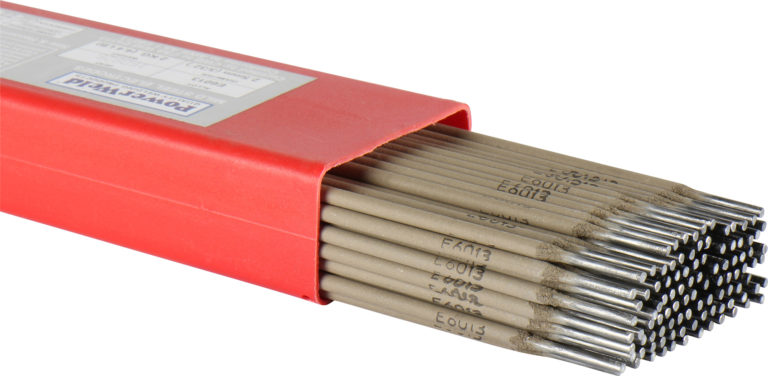
Commutator
The part of DC welding generator that converts AC supply voltage to DC welding output voltage is called Commutator.
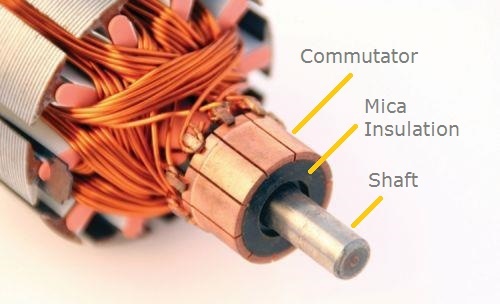
Tin and Lead
Principal materials used in soldering are Tin and Lead
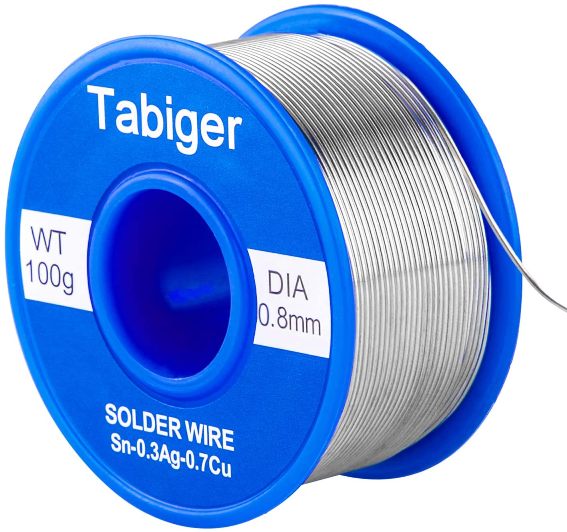
3:1
Thermit Welding is a welding process utilizing heat generated by exothermic chemical reaction between the components of the thermit (a mixture of a metal oxide and aluminum powder). The molten metal, produced by the reaction, acts as a filler material joining the work pieces after Solidification.
In Thermit welding process, iron oxide and aluminium oxides are mixed in the ratio 3:1.
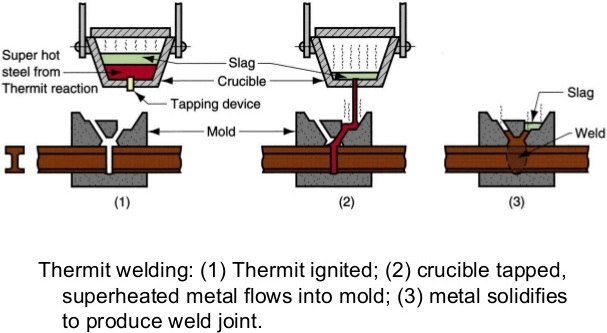
Front body of the welder
An apron is a safety accessory used to protect front body of the welder.
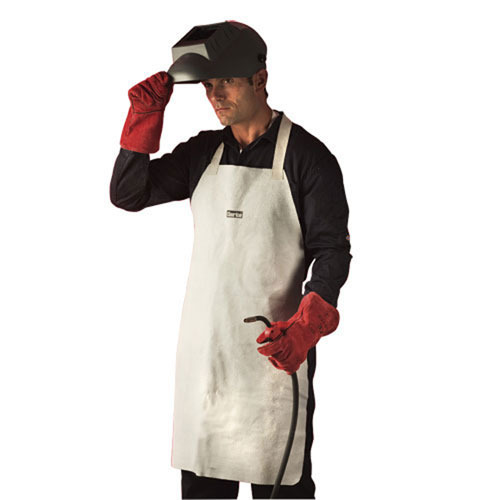