The flux commonly used in brazing is Borax
A flux is required for all brazing and soldering applications.
The purpose of the flux is to remove oxides from the base material and to prevent oxidation during the heating process, thus promoting the free flow of the brazing filler metal.
Brazing is essentially similar to soldering but it gives a much stronger joint than soldering. The principal differences is the use of a harder filler material, commercially known as spelter which fuses at some temperature above red heat, but below the melting temperature of the parts to be joined.
In Brazing most commonly used flux is “Borax” for ferrous and non-ferrous metals. It removes rust and prevents atmospheric effect, when brazing operation is going on
144) The flux commonly used in brazing is
borax
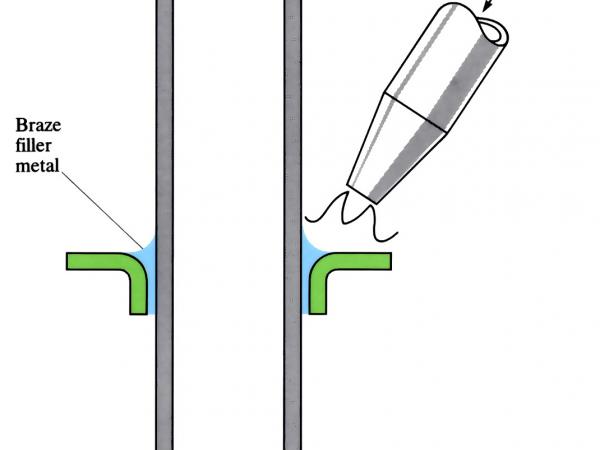
Related Workshop Technology MCQ with Answers
sheradising
Sherardizing is the formation of a corrosion-resistant, zinc-iron alloy coating, on the surface of steel or iron.
The method involves the heating of the object in an airtight container that has zinc powder.
A thermal diffusion process occurs and the zinc diffuses into the object’s metal surface, forming the zinc-iron alloy.
process of coating zinc by hot dipping
Galvanizing is a process of coating zinc by hot dipping.
anodizing
Anodizing is an electrochemical process that converts the metal surface into a decorative, durable, corrosion-resistant, anodic oxide finish.
Aluminum is ideally suited to anodizing, although other nonferrous metals, such as magnesium and titanium, also can be anodized.
forging
old chisels are forged to shape and hardened and tempered at the cutting edge. Although the vast majority of cold chisels are made of steel, a few are manufactured from beryllium copper, for use in special situations where non-sparking tools are required.